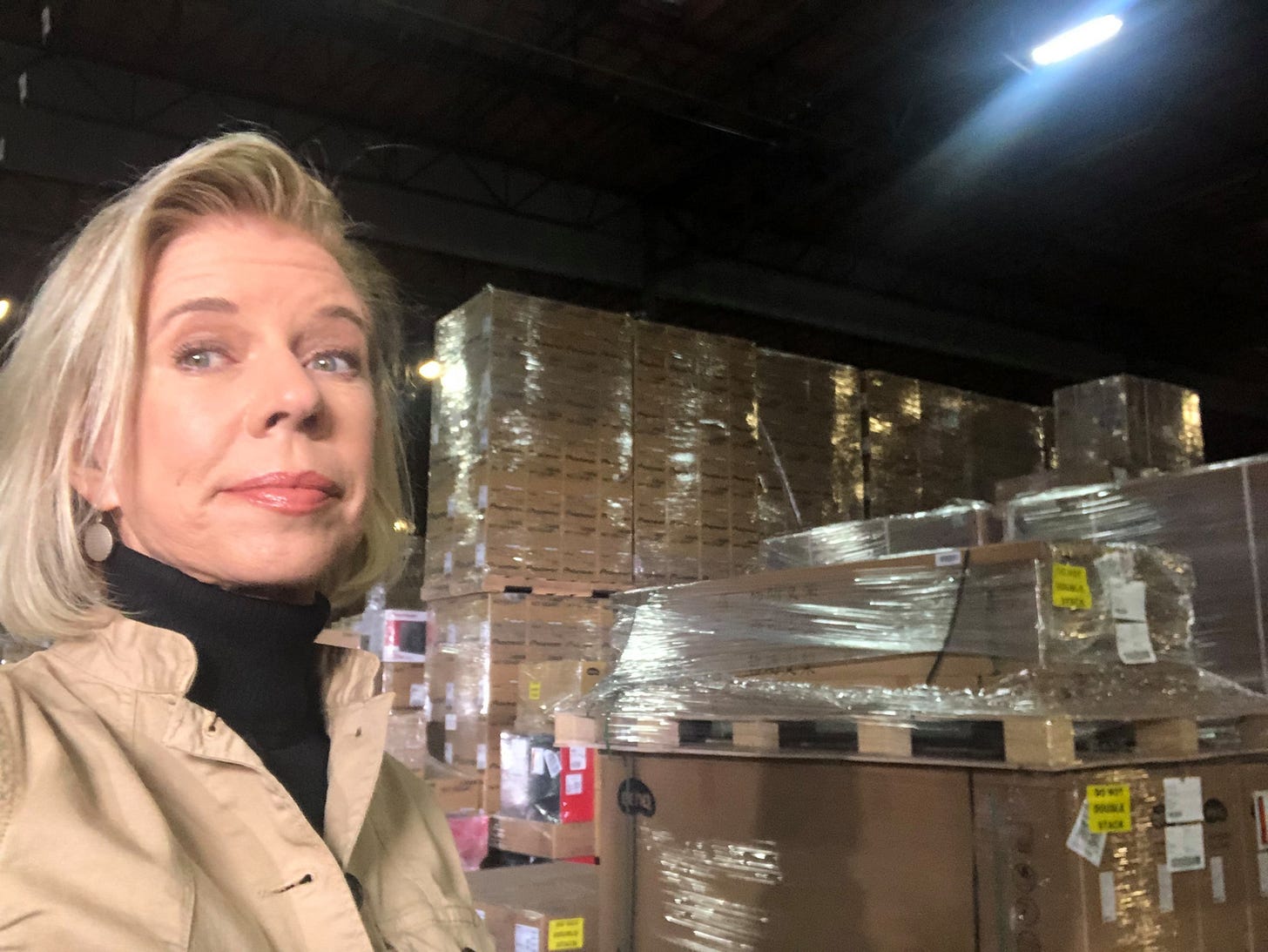
Keep up with me on Twitter, Facebook, Instagram and LinkedIn. Or subscribe here to receive my stories in your email box. It’s free.
I keep hearing that one reason the supply chain crisis can’t be unclogged is because there’s a lack of warehouse space.
Here’s the theory: cargo can’t be taken off ships at the ports because there’s no room on the docks, because truckers aren’t taking containers to warehouses, because the warehouses have no space.
So I went to a warehouse for CNBC to see if there was any space.
There is space.
“It’s not very busy,” says Gustavo Padilla, a veteran of the logistics industry who is currently director of operations for the iDC warehouse I visited. “Right now we should be very crowded.”
This 330,000 square foot warehouse in Lynwood is owned by Duke Realty, a publicly-traded warehouse real estate investment trust. It’s close to the ports of Los Angeles and Long Beach. Trucks arrive here and drop off containers filled with goods. The boxes of TVs and fake Christmas trees are then picked up by other trucks to deliver to stores or distribution centers further inland.
However, not as many trucks are coming from the ports as expected during this glut, and it’s taking longer for other trucks to come pick up the goods. Padilla says boxes which should be on the warehouse floor for only a day or two are spending as long as a week here.
Here’s what I saw with my own eyes.
NOT ENOUGH TRUCKERS
We’ve never needed so many truckers, and the shortage which existed before Covid has now become a crisis. Truckers are limited by how many hours they can work. However, despite reports suggesting otherwise, a new law in California that could end the owner-operator model for independent truckers is tied up in court and is not an issue yet. I also can’t find any evidence that a new rule mandating cleaner-burning truck engines by 2023 is the reason why there aren’t enough truckers in 2021.
NOT ENOUGH LABOR, PERIOD.
Truck deliveries to the warehouse I visited are so inconsistent that even though iDC is running two shifts, it’s only using half the normal manpower. Instead of 80 people a shift, Padilla says, “Right now the first shift is running probably about 40 [people], the second shift’s probably running about 30.” That’s probably a blessing, because even though Padilla tells me they’ve raised pay, it’s still a struggle to find labor. “If we ask for, let’s say, 10-20 people, we will get three.”
AND THE BIGGIE: THE EMPTY CONTAINER FIASCO
Empty containers litter the landscape. Some “empties” are parked on state land under an overpass next to the iDC warehouse, where it may take two weeks for trucks to remove them.
Here’s how screwed up it is.
— Screwup #1: An empty container sits on a chassis, or trailer, which is a huge problem. Chassis are in high demand, because you can’t go pick up a full container at the port without one.
— Screwup #2: Truckers are not able to get an appointment at a port terminal to return an empty container — and free up that chassis— because the terminals have no room for the empty container. Space is taken up by full containers… and other empties that can’t get on a ship until the ship can find room to unload its cargo (do you see how insane this is?).
— Screwup #3: The ports of Los Angeles and Long Beach lease space to about a dozen terminal operators. These are privately owned companies, and they have individual rules about who can pick up what and when. So far, there’s no visible effort to coordinate the return of empties/chassis by letting a trucker bring a container back to *any* terminal that has space, regardless if it belongs there (yes, different shippers have different containers).
READ THIS THREAD.
Ryan Peterson is CEO of Flexport, which moves freight. He took a boat around the port to see for himself what’s happening, and he suggested some solutions to “overwhelm the bottleneck,” like:
— Temporarily change rules in truck yards so that more than two empty containers can be stacked on top of each other. This would free up chassis.
— Use all the available National Guard chassis on a temporary basis.
— Create a container yard on government property near a large rail hub within 100 miles of the port and have trains go back and forth bringing containers there. Then direct trucks to that yard to pick up cargo instead of the ports.
It’s an excellent Twitter thread which I highly recommend.
“It’s going to get worse before it gets better,” Gustavo Padilla tells me. Look, I know there are issues all along the supply chain. I know it’s a complex problem. But I have a nagging suspicion that the way business has been done around the port complex was problematic long before the pandemic, employing an inefficient set of rules and procedures that should have been changed long ago to withstand this surge in American consumer demand (or at least handle it better).
To quote Warren Buffett, “Only when the tide goes out do you discover who’s swimming naked.”
Of course, with shipping prices skyrocketing, maybe there are parties involved who are in no rush to improve efficiencies.
Just sayin.’